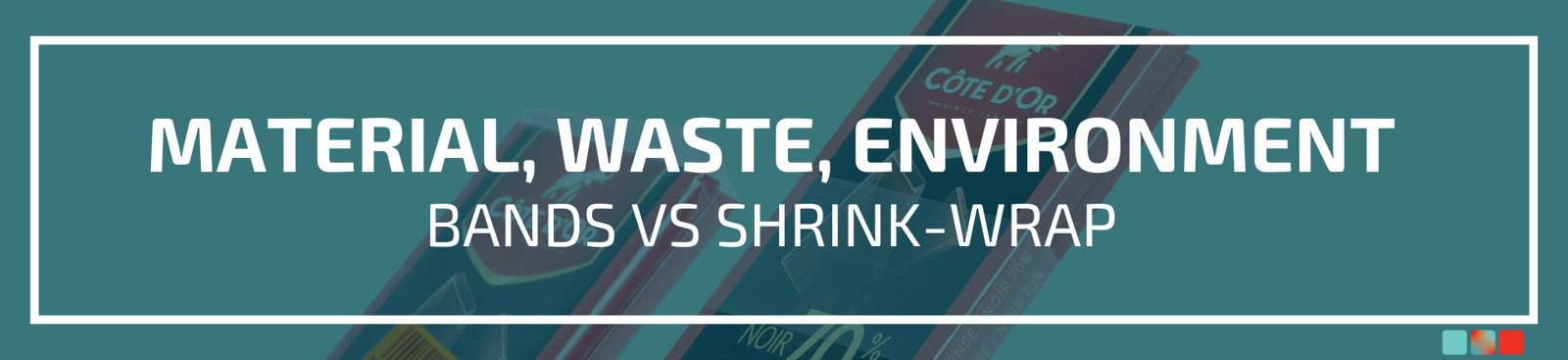
Material use and packaging waste
In our previous blog, "Bands vs Shrinkwrap: Why Application Matters", we unpacked how these two packaging solutions differ in their method of application and operational implications. The results were telling: banding offers a faster, cleaner, and more efficient application process, while shrinkwrap tends to be slower, more labor-intensive, and reliant on multiple steps and machines.
But the story doesn’t end with application.
Another crucial, and often more impactful, aspect is material usage. When packaging a product, it’s not just about securing the contents. It’s about how much material is used in the process, and more importantly, how much of that material is discarded as waste.
So how do bands and sleeves stack up when it comes to material efficiency and waste reduction? Let’s take a closer look.
Full coverage vs. smart coverage
Shrinkwrap takes the "cover-all" approach. It completely covers a product in plastic, using a layer of film that is wrapped and then heat-sealed to tightly conform to the product. While this method creates a uniform and tamper-evident finish, it comes with significant drawbacks:
- Heavier material consumption: Wrapping an entire product surface demands large quantities of plastic film, especially for items with complex shapes.
- Higher energy expenditure: The heat-shrinking process consumes considerable energy, requiring both machinery and time.
- More post-use plastic waste: Once opened, the entire wrap becomes single-use waste.
In contrast, banding offers a minimalist solution. Instead of wrapping/covering the whole product, banding uses a strip of paper or film, just enough to secure and seal the product. This narrow band, applied with optimal tension, holds items together reliably without over-packaging.
Less material = less waste
It’s a simple equation: the more packaging material used, the more waste generated. Shrinkwrap, by its nature, falls on the heavier side of this equation. Once a product wrapped in shrink film is opened, all that plastic becomes single-use waste.
This discarded material doesn’t vanish. It needs to be collected, sorted, and processed which can be a costly and labor-intensive process before it even reaches the recycling phase. Because shrinkwrap completely covers each product, it not only increases the volume of waste but also adds unnecessary strain to recycling infrastructures already under pressure.
Banding offers a sustainable and streamlined alternative to shrinkwrap. By covering only a small section of the product, a band generates significantly less waste. This minimalist approach not only reduces the volume of discarded material but also simplifies recycling. Less plastic (or paper) means easier sorting, faster processing, and lower costs for recyclers and manufacturers alike.
Better compatibility with circular packaging
Material efficiency isn’t just about using less, it’s also about using smarter. As sustainability expectations rise, recyclability and reusability are just as critical as reducing material volume.
Why banding supports circular packaging goals:
- Recyclable materials: Banding material is made from paper or film, both easily recyclable.
- Supports mono-material packaging targets: Ideal for meeting environmental regulations across the EU and beyond.
- Material matching: Paper bands for cardboard trays, film bands for plastic containers. This enhances compatibility and recycling efficiency.
- Simplified sorting: A more uniform packaging structure increases the likelihood of correct recycling and reduces contamination risk.
- Design with intent: Small material choices lead to large sustainability gains.
Where shrinkwrap falls short:
- Limited material flexibility: Shrinkwrap is always plastic/film.
- Incompatible with mixed packaging: When wrapped around paper/cardboard, the combo no longer qualifies as mono-material.
- Recycling complications: Mixed materials make sorting harder, reduce recycling efficiency, and may disqualify packaging from some recycling streams.
Efficiency redefined: Do more with less
Shrinkwrap may get the job done, but it often does so at a cost. It's material-heavy, energy-intensive, and functionally limited. While it can effectively seal and bundle products, that’s where its utility ends. Any additional requirements, such as branding or labeling, must be handled separately. That means more materials, more production steps, and ultimately, more complexity and cost.
Banding, by contrast, redefines efficiency. With just one paper or film band, you can bundle, seal, label, and brand in a single motion. Whether it’s adding a logo, barcode, ingredient list, or promotional message, it can all be printed directly onto the band. This integrated approach cuts down on packaging layers, shortens production timelines, and reduces both material and labor costs.
Material matters more than ever
In today’s rapidly shifting regulatory landscape, where environmental accountability and resource efficiency are no longer optional, how much material you use, and how it fits into a product’s end-of-life cycle, matters more than ever.
Shrinkwrap may still be a familiar sight, but familiarity doesn’t equate to future-readiness. With its excessive material use, high energy consumption, and limited functionality, it stands on uncertain ground, especially as packaging regulations become more strict and sustainability expectations rise.
Banding, on the other hand, is already aligned with the direction packaging is headed. It’s a leaner, more resource-efficient solution that not only uses less material and generates less waste but also integrates multiple functions into a single step. More importantly, it fits seamlessly into circular economy models and meets the growing demands of environmental legislation.
Questions about our banding solutions?
Together we can find opportunities to optimize your packaging.
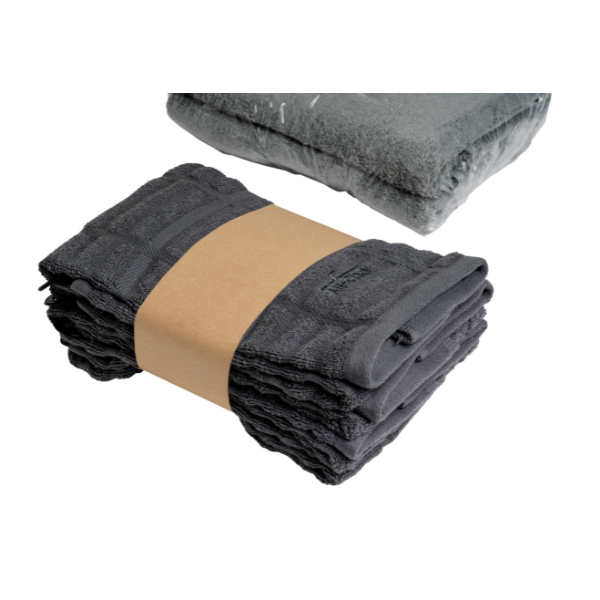
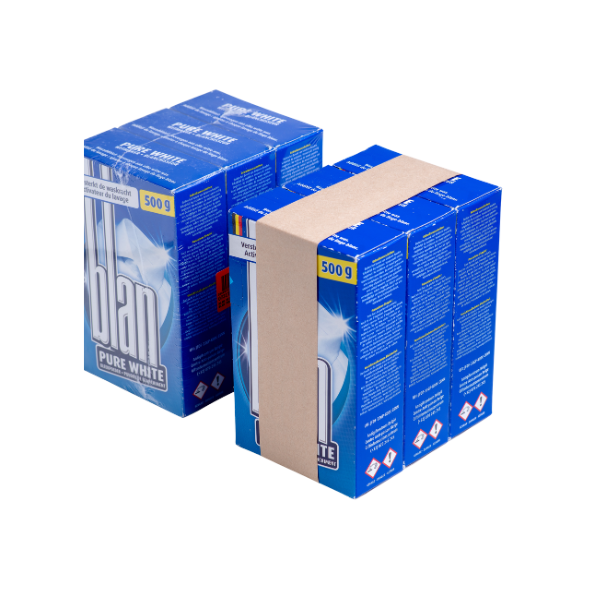
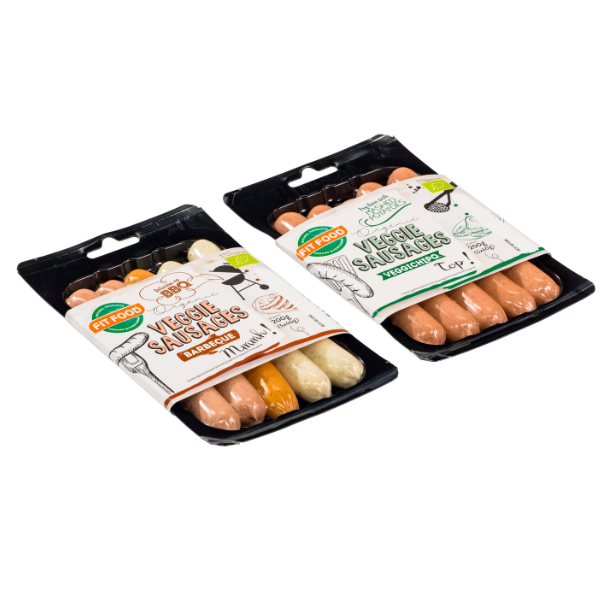
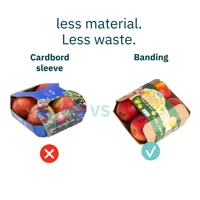
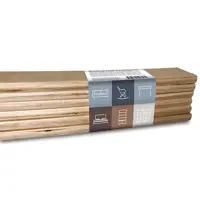
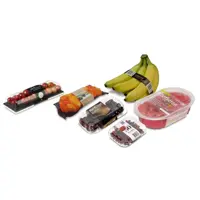
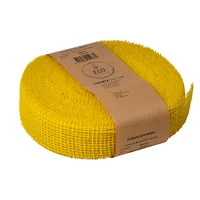
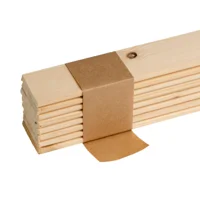
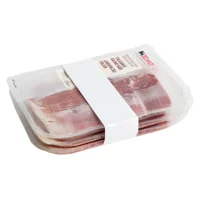
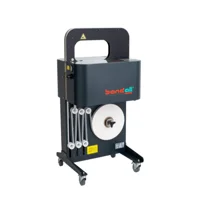