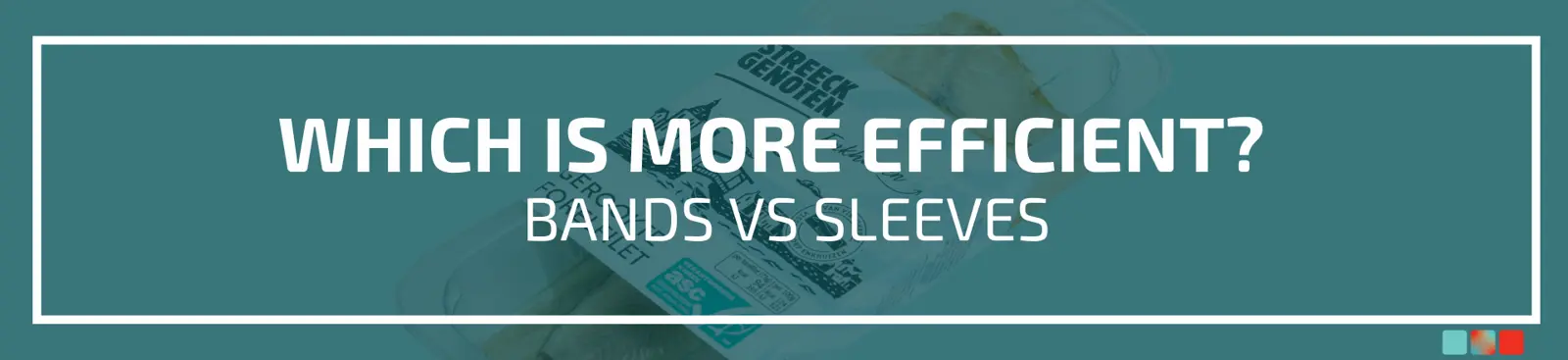
How do cardboard sleeves and bands differ in efficiency?
Maximizing efficiency in packaging is key to boosting productivity and achieving your business goals. When it comes to cardboard sleeves versus banding, there are clear differences in how each solution stacks up in terms of efficiency.
Let’s dive into how these two packaging options compare, focusing on factors like the application process, product fit, labor requirements, printing capabilities, and more.Application: Machine vs man
The most significant distinction between banding and sleeves lies in how they are applied to a product. Banding is an automated process, where specialized banding machines apply bands to products in a precise and systematic manner. These machines come in various models, ranging from plug and-play machines ideal for small tasks to fully automatic machines designed to speed up processes and for large-scale production.
On the other hand, cardboard sleeves are applied manually, requiring manual labor to position and secure each sleeve onto the product. This process can be time-consuming and may introduce inconsistencies in alignment and fit. While manual application allows for greater flexibility in handling unique or irregularly shaped products, it can also increase labor costs and lead to not meeting demand.
Fit and presentation: neat vs loose
The way packaging is applied has a significant impact on the product’s appearance and presentation. With banding, the packaging process is automated, ensuring that bands are applied systematically and securely. This creates a tight, precise wrap around the product, preventing any shifting during transport and on the shelf. Furthermore, many banding machines can be configured with advanced positioning technology, allowing for accurate alignment of key details. For example the logo on top of the packaging and the barcode on the side. This ensures a uniform presentation and ensures your packaging looks perfect every time.
In contrast, cardboard sleeves are typically applied manually and often fit more loosely around the product. Designed to be slightly larger for easier placement, this looser fit can lead to misalignment during application and transport. As a result, the packaging may shift, leading to a less professional presentation. Furthermore, sleeve application depends on manual precision, increasing the risk of inconsistencies in positioning, creasing, or tearing, which could affect product appeal on the shelf.
Labor efficiency: Automated vs manual
As mentioned earlier, banding is an automated process powered by a banding machine, making it far less labor-intensive. Banding machines can operate continuously with minimal supervision, significantly reducing the need for manual intervention. This not only speeds up production but also enhances consistency, as automation eliminates human error.
Cardboard sleeves, however, rely on manual labor to place them around the product, creating a more resource-heavy process. This dependence on human workers means that factors, such as fatigue, absenteeism, or inconsistencies in application, can impact efficiency and quality. Manual application also slows down production speed, making it less suitable for high-volume operations.
Custom printing: On-demand vs pre-printed
When it comes to custom printing, the differences between banding and cardboard sleeves become even more evident. Cardboard sleeves are typically pre-printed in bulk, which limits flexibility when adding on-demand information like batch numbers, expiry dates, or unique barcodes. Each time new data needs to be included, additional steps, such as labeling, are required which slow down the process and increase reliance on manual work.
Banding, however, offers a more streamlined and adaptable solution. Many banding machines can be configured with built-in printers, enabling on-the-spot printing of essential details directly onto the band as it is applied. This integration of packaging and printing into a single step not only cuts down on labor but also minimizes errors associated with manual data entry or sticker application. Moreover, this on-demand printing capability allows for greater flexibility in product labeling, reducing material waste and improving overall efficiency.
Final verdict
The key differences between banding and cardboard sleeves in terms of efficiency stem primarily from the application process and adaptability. Banding, being an automated process, streamlines packaging by reducing labor requirements, ensuring precise positioning, and seamlessly integrating labeling within the same step. This makes it a highly efficient solution, particularly for industries requiring speed, accuracy, and flexibility.
In contrast, cardboard sleeves, which are applied manually, demand more labor and can introduce inconsistencies in alignment and fit. Their larger size and need for pre-printing also add complexity to inventory management and customization. While both options have their uses, only one options seems more future proof and scalable for businesses looking to optimize their packaging process.
Questions about our banding solutions?
Together we can find opportunities to optimize your packaging.
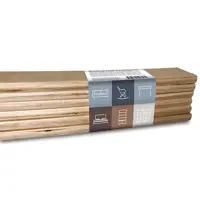
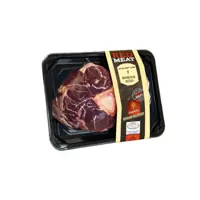
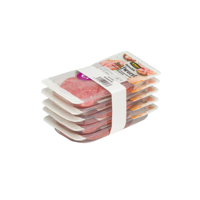
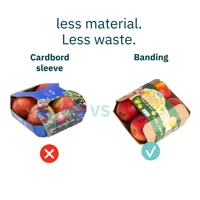
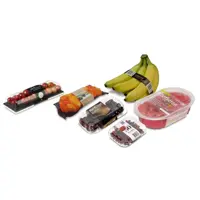
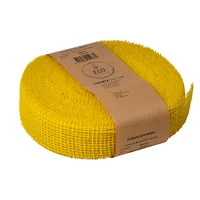
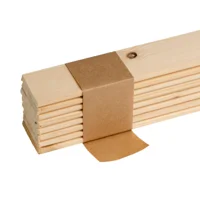
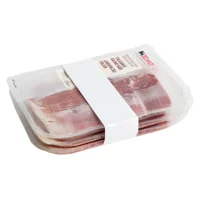
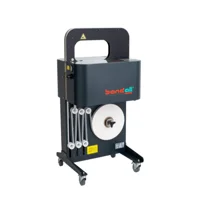