Save 80% in materials by banding
With the current shortages in raw materials, it is important to be economical with the materials available. A band can positively contribute to this. By switching to banding for the packaging, bundling, or labelling process it helps achieve huge reductions in materials. Percentages of 80% are no exception. Switching to banding does not only ensure a reduction in materials, it also has a positive impact on the costs and sustainability of your packaging.
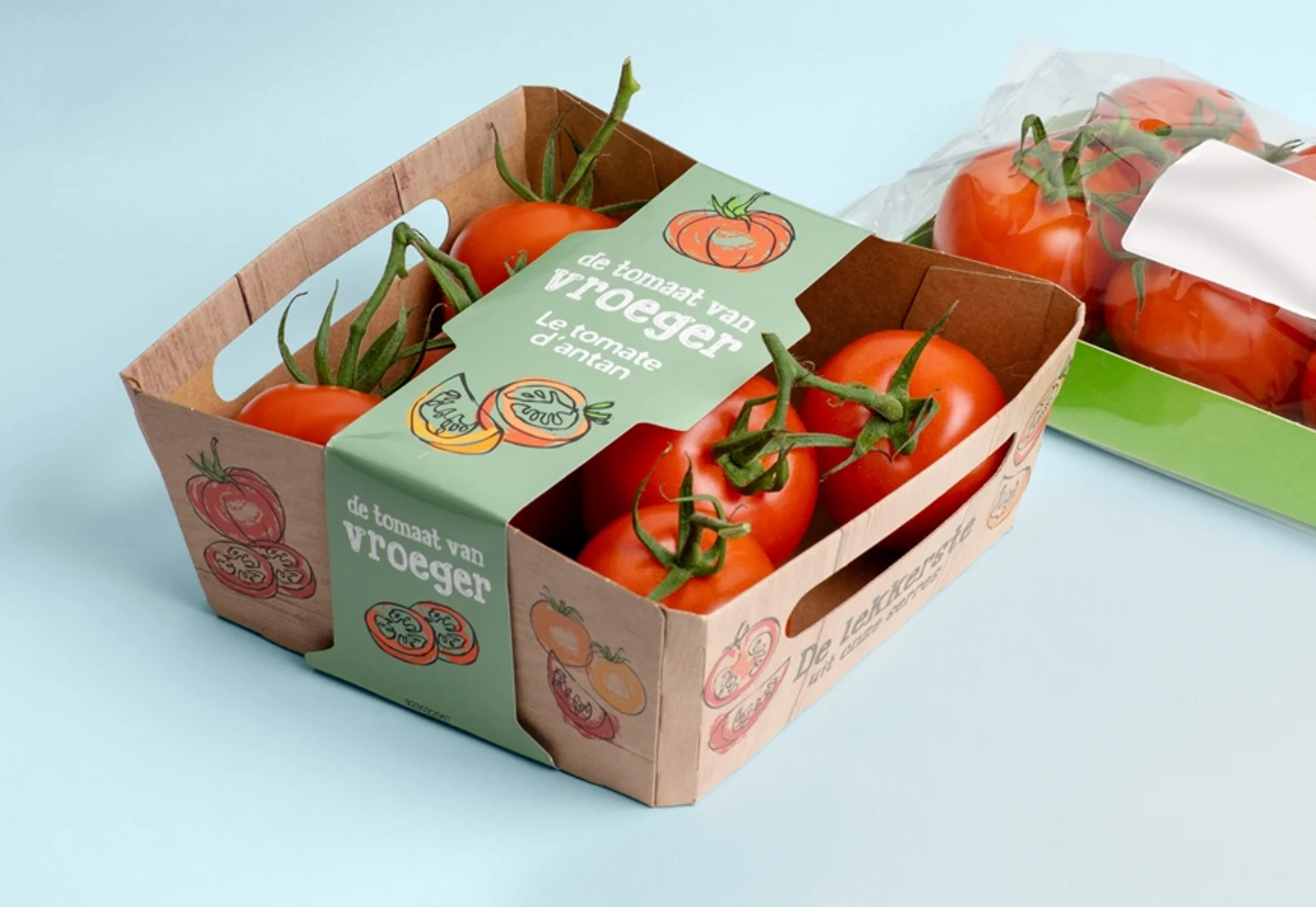
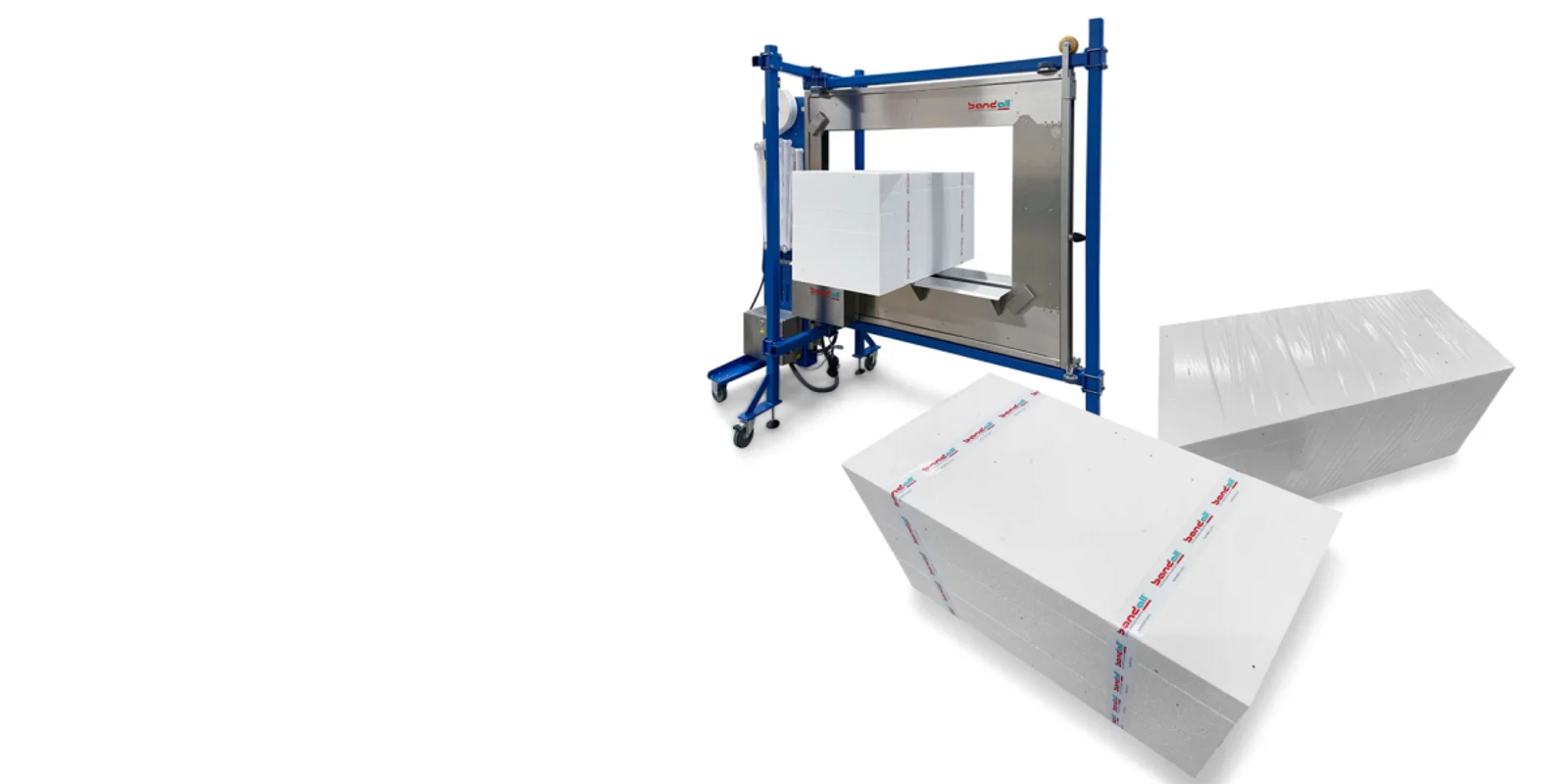
Minimum use of materials
Banding has many applications. Whether it’s bundling, labelling, tamper evident sealing or a combination of these applications, in almost all cases it leads to more sustainable packaging. Moreover, banding ensures that many additional packaging elements are no longer needed. Think of elastic bands, clips, tape or self-adhesive labels. Less is more!
A good example is in the EPS industry. EPS plates - often used for construction or industry - are often fully wrapped in shrink film. However, is this really needed? A Danish producer has been able to save 74.7% in materials, by switching to Bandall banding. In other markets as well, banding makes outer cartons, plastic bags and shrink film unnecessary.
Material saved by banding per industry:
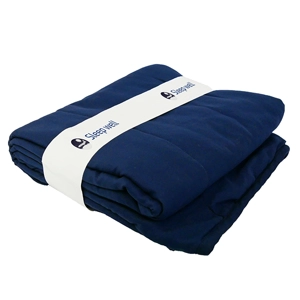
92.4% reduction
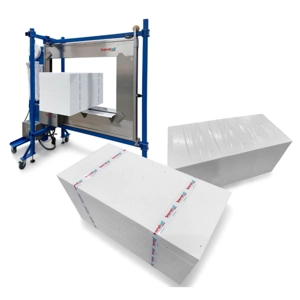
74.7% reduction
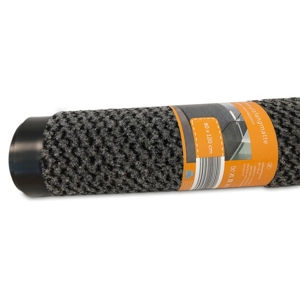
75% reduction
Less waste with smart printing technology
Printing variable information during the banding process also leads to less waste. For example, a small change in product description or nutritional values, automatically means you have to throw away all your labels in stock. This is the strength of printing during the banding process. It makes your packaging process more flexible and more sustainable.
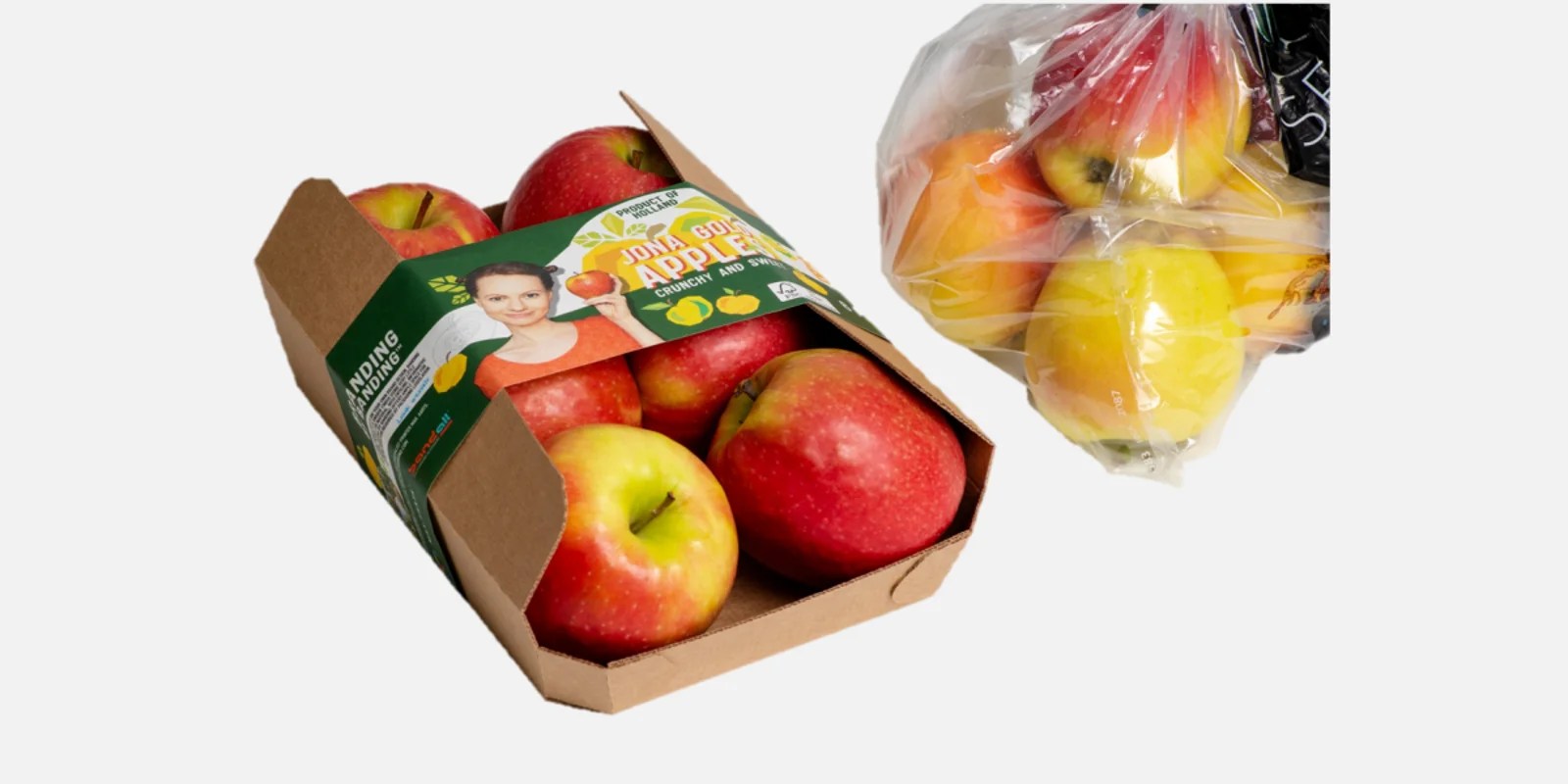
Social impact
At Bandall we see it as our social duty to encourage companies to think differently, to inspire them and to make them aware of their social impact.
Start saving material too!
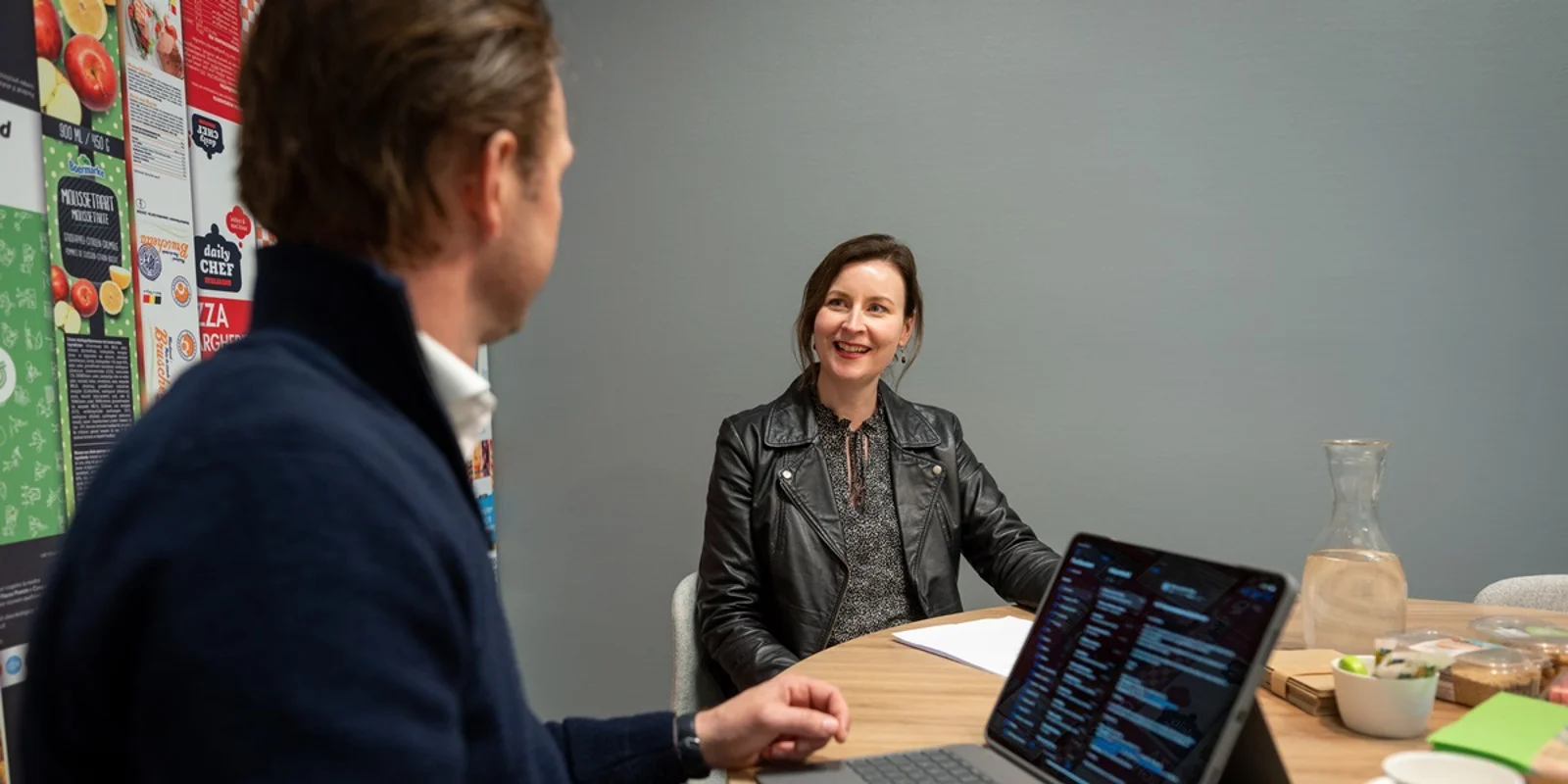