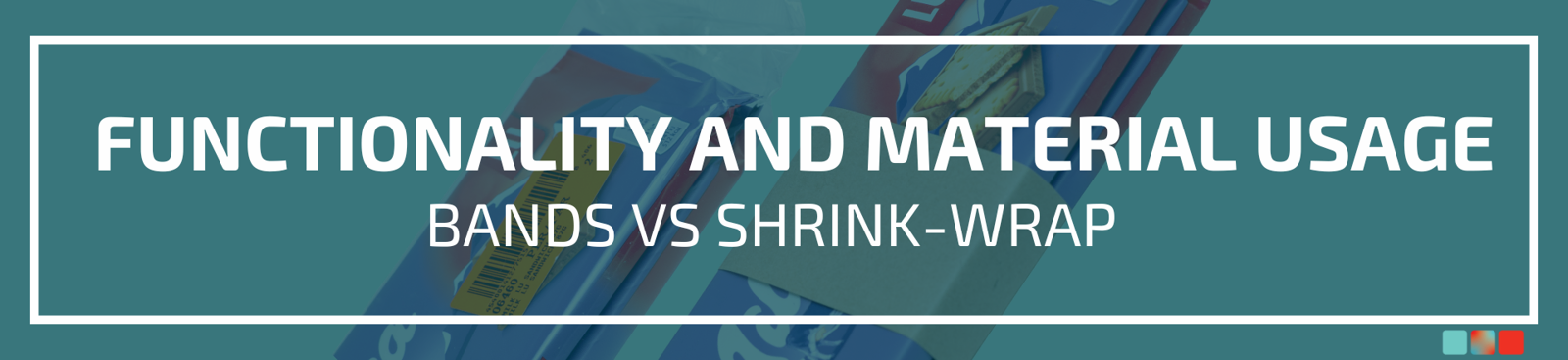
Efficiency redefined: Do more with less
In the world of packaging, efficiency isn’t just about speed. True efficiency is about getting more done with less material, less energy, and fewer steps. It’s about building smarter systems that reduce waste, cut costs, and improve performance from start to finish.
When comparing banding and shrinkwrap, the difference becomes clear in how much each solution can accomplish with the material it uses. In this blog, we’ll take a closer look at their capabilities and explore which solution delivers greater results with fewer resources.
Minimal input, maximum function
Shrinkwrap may get the job done, but it demands a lot to do so. The process typically requires:
- Multiple machines
- Heat for application
- Full plastic coverage
- A multi-step workflow
The outcome? A fully enclosed product packaged in plastic.
Banding offers a packaging solution that it requires fewer steps, machinery and material:
- A single machine
- A strip of paper or film
- No heat required
- Bundling, branding and labeling applied in one step
Efficient product bundling
Both shrinkwrap and banding are capable of bundling products, but how they accomplish this task differs significantly in terms of efficiency and sustainability.
Banding secures products using a thin strip of paper or film, applied at optimal tension to hold items together firmly. Whether bundling a single item or stacking multiple products, the band wraps securely around just a portion of the product or stack. This provides a sufficient hold without the need for full coverage. This method minimizes material use while maintaining a secure seal and enhancing product presentation. Banding machines can even be equipped with bundle press units, ensuring tighter and more uniform stacks that stay intact during storage or transport.
Shrinkwrap, on the other hand, requires a much more intensive approach. It fully encloses each product in plastic film, which is then heated to conform to the shape of the bundle. While this can also achieve a tight seal, it demands more material and energy to do so. Furthermore no branding or labeling is added to the product during shrinkwrapping.
Recyclability: Designing for the circular economy
As new packaging regulations emerge, a key focus is enabling a circular economy. This is where packaging is designed to be reused, recycled, and kept in the loop resulting in far less packaging being produced and majority of it being reused. While shrink-wrap might appear recyclable at first glance, it often complicates the recycling process due to its excessive material use.
Why shrinkwrap falls short:
- Uses more material than necessary around each product
- Adds volume to the recycling stream
- Makes sorting and processing more complex
In contrast, banding is purposefully designed to support a circular economy:
- It requires significantly less material per product/stack
- Bands are sleek and easy to separate for recycling
- Banding is ideal for mono-packaging (e.g. paper band + cardboard tray or film band + plastic container), making sorting easier and recycling more efficient
Packaging that’s built for what’s next
As the packaging landscape evolves, the need for solutions that align with efficiency, minimalism, and recyclability are becoming more prominent.
Shrink-wrap, while still widely used, struggles to meet these rising standards. Its reliance on excess plastic, energy-intensive application, and unoptimized recyclable design place it at odds with the direction that law and the global market is heading.
Banding, on the other hand, is already ahead of the curve. It uses less material, offers flexible options in both paper and film, a more efficient packaging process and supports circular economy practices.
Questions about our banding solutions?
Together we can find opportunities to optimize your packaging.
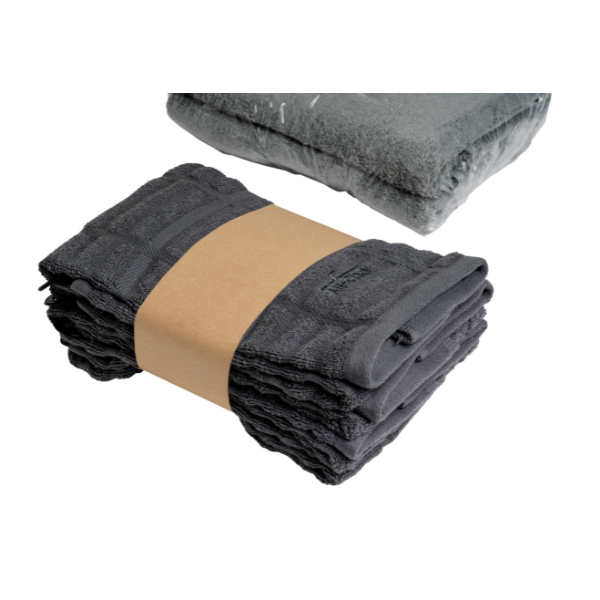
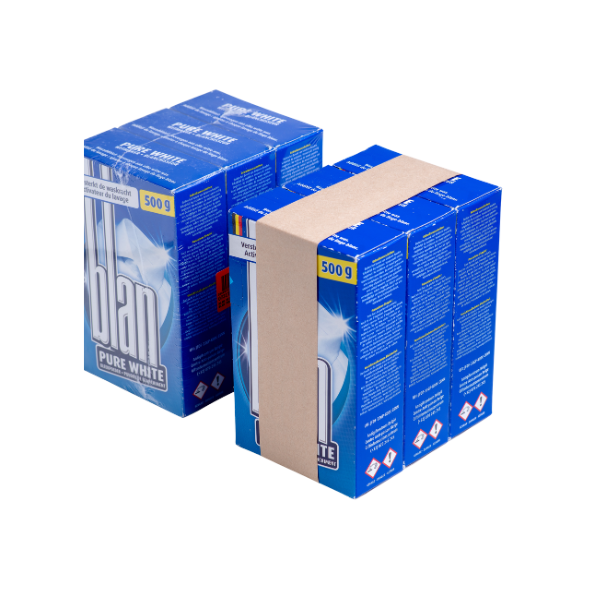
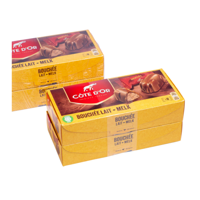
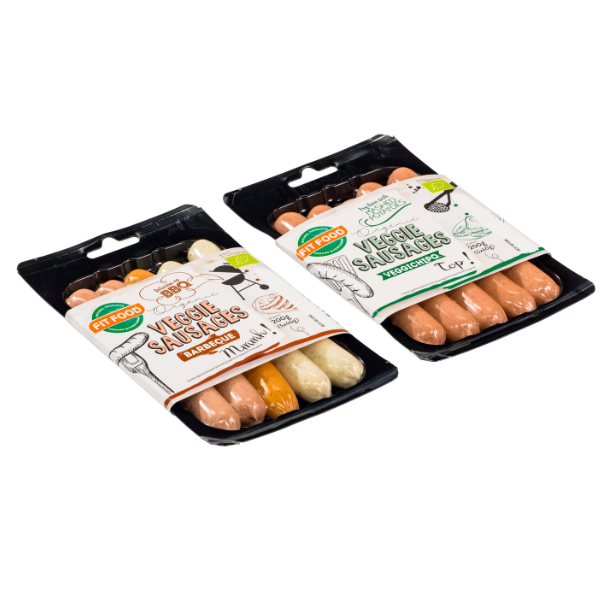
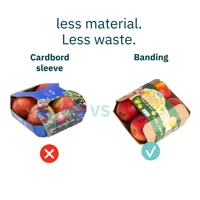
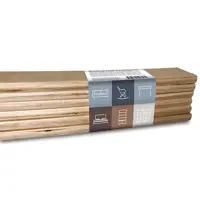
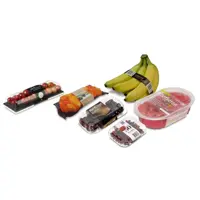
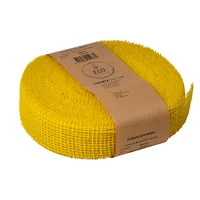
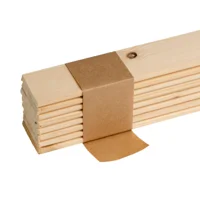
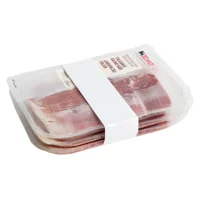
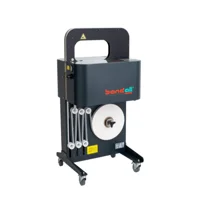