Printing companies can position themselves sustainably with banding
In the graphics industry, banding has been replacing other ways of bundling and packaging printed materials. Banding has a number of important advantages: it saves materials, costs, and is more environmentally friendly than other bundling methods.
Banding has many environmental benefits
Previously, a stack of printed materials was usually bundled by a hard plastic strap or foil. Through the years, banding became increasingly popular. It offers a number of significant advantages. Banding allows for the use of a paper or mono-film band of BOPP, which is recyclable in both cases. This is not possible with a strap, which also increases the risk of damage to the printed products. In addition, a band requires much less packaging material compared to shrink film or an expensive cardboard box, which can also be used as a bundling method. Finally, banding is also much more energy efficient than using shrink film. “Our banding machines only use 1 kWh or even 0.5 kWh. A shrink film tunnel, on the other hand, uses 10 kWh.” With all these environmental benefits, a company in the graphics industry can perfectly position themselves as ‘green’ to its customer.
Another advantage of a band is that it can be used as a flexible communication tool, without the need for an additional label. This applies to both a pre-printed or an unprinted band, which can be provided with additional information during the banding process. Think of a barcode, QR code, or other personalized messages.
Stand Alone and fully automatic
Bandall still supplies a relative large number of Stand Alone machines for the Post Press Print finishing of commercial printed products. This is because in practice these machines are quickly moved from for example the cutting machine to the folding machine. For labels and In-Mould labels, Bandall machines guarantee a neat and tight bundle of standard labels or multi-shaped, and wafer thin In-Mould labels. Thanks to the advanced vacuum feed system of the machines, this is possible at high speeds without damaging the labels. They are available in a Stand Alone version, but also as a fully automatic banding line, which can be expanded with a press or a label line.
The banding machine is unique for banding banana-shaped labels in two places – front and back – thanks to a patented technique. Partly because of this, Bandall can count the largest producers of wafer-thin In-Mould labels in the world, among its clientele. Bundling and banding machines are offered to the cardboard industry quickly and without damage, bundle stacks of plano cardboard packaging or luxury cardboard. Meaning, without any damage to the corners and edges. A fourth market is banknotes and valuable papers with special printing and finishing techniques. In this market, damage free bundling is even more crucial.
Do you want to elevate your packaging?
Together we can find opportunities to optimize your packaging.
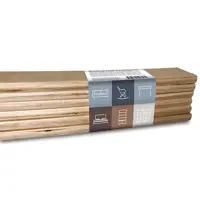
Applications of banding
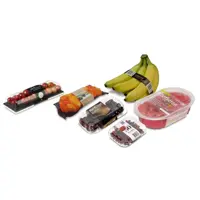
Benefits of banding
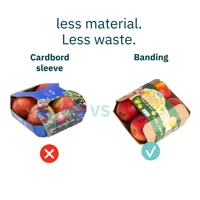
Banding vs. other solutions
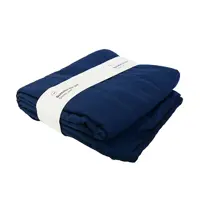
10 Reasons to switch to banding
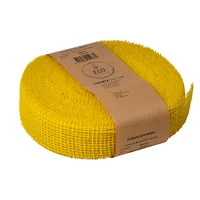
Zwartz - From shrink wrap to paper bands
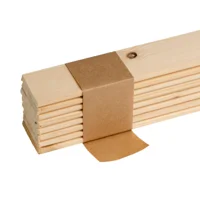
Novatrade - Improved quality and efficiency
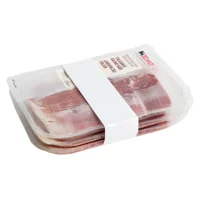
Packaging food products
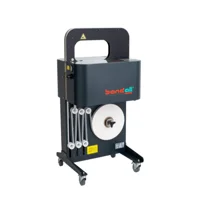