Klooster's bold leap into efficient packaging
For over a century, fish monger Klooster, a proud family-run business from Enkhuizen, has been perfecting the art of smoked fish. Known for their expertise in smoking, processing, and packaging premium fish products under both their own brand and for private labels, Klooster has built a reputation for quality and tradition. Recently, they took a bold step forward in their packaging process, embracing a new, more efficient solution that has transformed their operations. This change has led to unexpected advantages including boosting their efficiency, cutting down on resources, and optimizing their production flow.
Klooster’s quest for a smarter packaging solution
Processing smoked fish is no small feat. It’s a labor-intensive process that begins with brining and smoking, followed by the careful, manual filleting of each fish. Packaging, too, has traditionally been a hands-on task at Klooster. Cardboard sleeves were once manually wrapped around each package—a time-consuming step for their smaller batch sizes, which range from 500 to 1,000 products. While automation is possible, it’s not always practical for the scale at which Klooster operates. Tijsen, the commercial director at Klooster, explains, “The numbers simply don’t justify the cost of fully automating the sleeving process.” But Klooster was searching for something more—a packaging solution that not only maintained their artisanal quality but also allowed for eye-catching branding and greater efficiency across their production line.
Efficiency redefined
But with banding, things are different. This innovative approach offers the flexibility that Klooster needed. The banding machine can be easily adjusted to accommodate different tray sizes without the hassle of changing formats. With just one band width for all packaging, switching between products is seamless, and changing a roll is quick and straightforward.
“The banding process itself is remarkably efficient,” Tijsen praises. Operators simply place the packaged fish onto a supply belt, which carries the trays to the modular banding machine. Depending on the required speed, the machine can be equipped with one or more banding heads. Klooster opted for a double-head version, capable of handling up to 40 packages per minute. As the trays move through the system, a pusher guides them into position, and the machine does the rest—wrapping, tightening, sealing, and cutting the band in a single smooth motion before sending the trays off on a discharge conveyor. This streamlined process not only boosts efficiency but also delivers consistently high-quality packaging, perfectly suited to Klooster's needs.
How banding transformed Klooster’s operations
The impact of switching to banding has been transformative for Klooster. One of the most immediate benefits has been the significant reduction in warehouse and production space needed to store packaging materials. A single roll of banding paper replaces dozens of bulky boxes of cardboard sleeves, streamlining their operations and freeing up valuable space. The weight difference is also striking—each band weighs just 2 grams compared to the 25 grams of a sleeve, greatly reducing material consumption.
Additionally, the precision of the banding process ensures that each band is perfectly positioned, staying securely in place—an advantage over sleeves that can shift during handling. But perhaps the greatest benefit has been the speed. With banding, the packaging process is at least twice as fast as manually sliding sleeves around the trays. This boost in efficiency is critical for Klooster, as it aligns with their goal of achieving a return on investment within four to five years. Plus, the banding process is unaffected by humidity, guaranteeing consistent, high-quality results regardless of the environment.
Klooster thrives after switching to banding
Fish monger Klooster couldn't be more pleased with their decision to switch to banding. Reflecting on the transition, Commercial Director Jac Tijsen expresses his satisfaction: 'Since making the switch, we’ve thrived with a faster, more cost-effective packaging solution.' By replacing traditional sleeves with bands, Klooster has not only streamlined their packaging process but also set their products apart with unique, creative branding. Beyond efficiency, this move has steered the company towards a more sustainable future, perfectly aligning with their commitment to innovation and quality.
Ready to optimize your packaging process like Klooster did?
Let’s connect and explore the opportunities together!
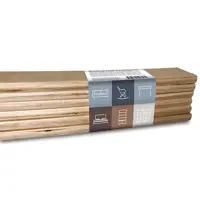
Applications of banding
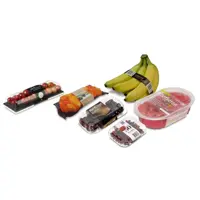
Benefits of banding
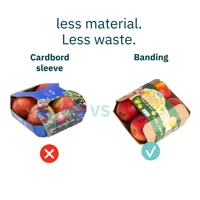
Banding vs. other solutions
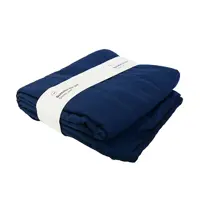
10 Reasons to switch to banding
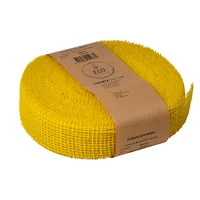
Zwartz - From shrink wrap to paper bands
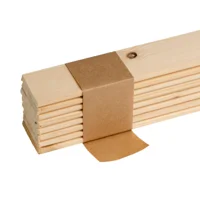
Novatrade - Improved quality and efficiency
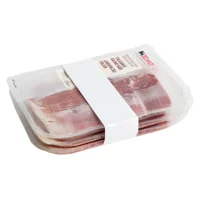
Packaging food products
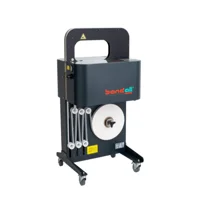