Ready for use thanks to banding
Efficiency for sustainable BVP packaging
Packaging supplier BVP has an innovative packaging for thermal insulation, the Papercooler. A client asked BVP to deliver these in an opened condition: ready for use. BVP found the best solution in a Bandall banding machine. A paper band ensures that the cardboard flaps of the packaging remain open. The moment the Papercooler has to be closed, the band can be removed easily and quickly.
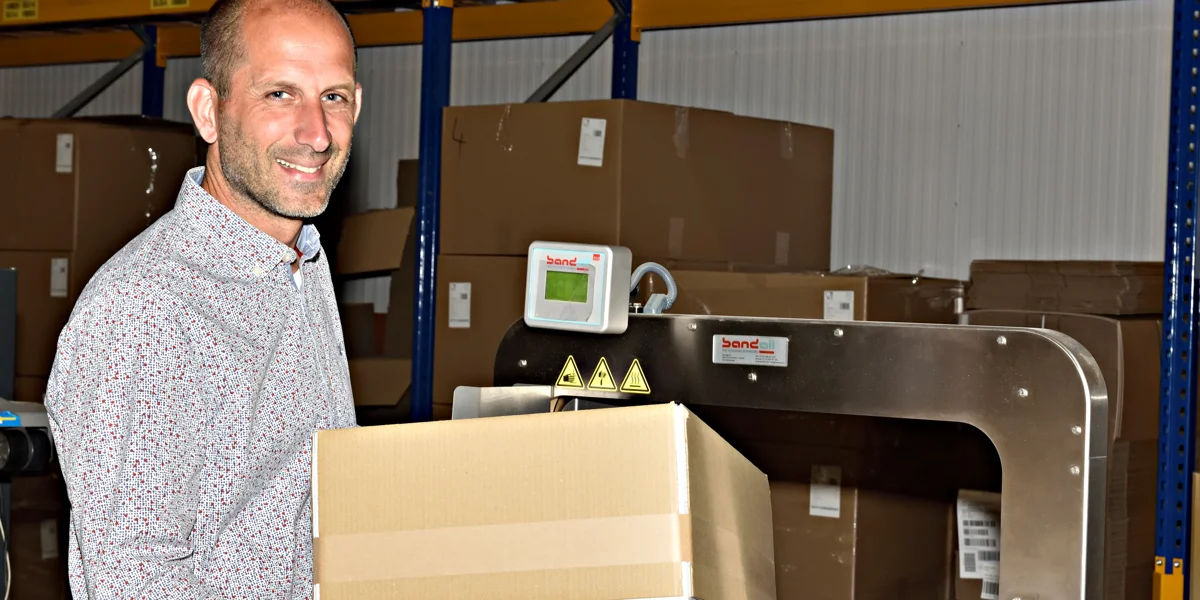
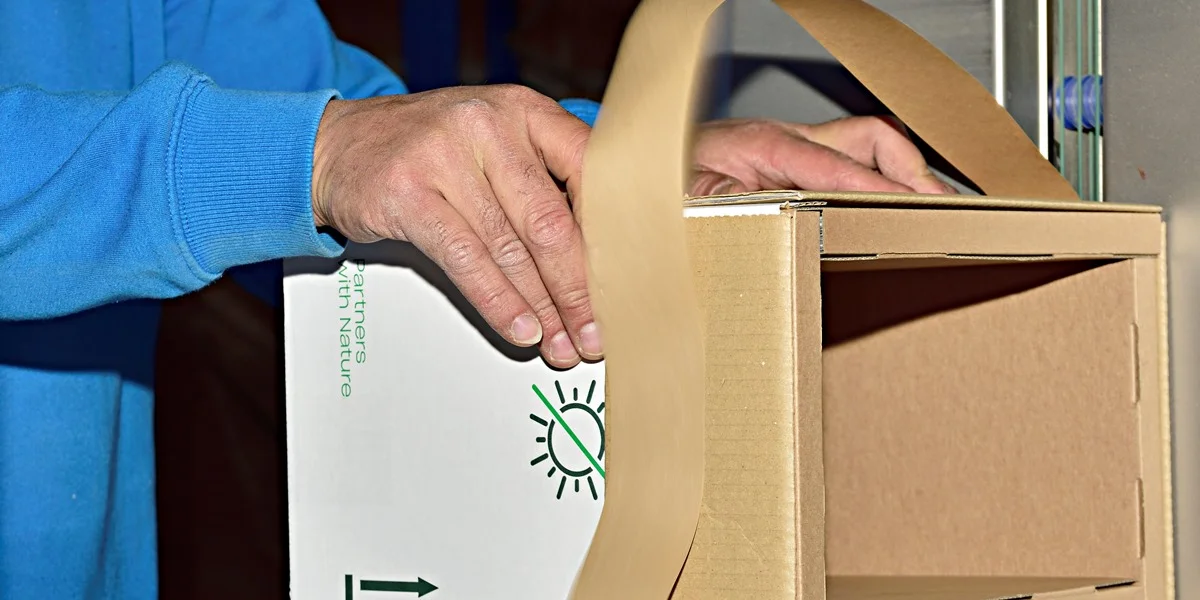
BVP supplies various packaging materials. Sustainability is a matter of course for BVP. They always challenge its customers to choose for the most sustainable solution. Such a way of working demands the company is able to offer something. And they do because they think ahead of the market. As a result, they regularly find new solutions to save material and transportation costs and discover new ways to reuse waste materials.
A special product from BVP is the Papercooler, a box that thermally insulates the contents and is made entirely of paper and cardboard. The walls of the box are made of several layers: a smooth inner wall, a smooth outer wall, and in between several layers of paper with an irregular ribbed structure. The ribbed structure creates cavities that are able to hold stagnant air. This ensures the high insulating value of the Papercooler, as paper and air are excellent insulators.
Maximum efficiency
The Papercooler was developed in cooperation with Thermo Fisher Scientific. The cool box consists of loose parts that can be quickly assembled due to their smart structure. However, for one customer, this was not quick enough. This customer wanted the boxes to be delivered ready-for-use. With a top that is folded open, so that employees can put the products in right away. Close, ship and done. The company ships a lot of packages. Which is why every part of the process counts. Every step that can be saved, increases the efficiency of the logistic process.
This client is Koppert, a company that supplies insects, mites, bumblebees, and fungal spores to farmers and horticulturalist all over the world to control pests and pollinate plants organically. During transport, the temperature should not deviate too much, otherwise the insects will not survive the journey. That is why Koppert, like many other companies, used EPS packaging. However, EPS does not fit with Koppert's aim of achieving a sustainable working method. Which is why the company was looking for a more sustainable packaging solution; a solution that does not use plastic.
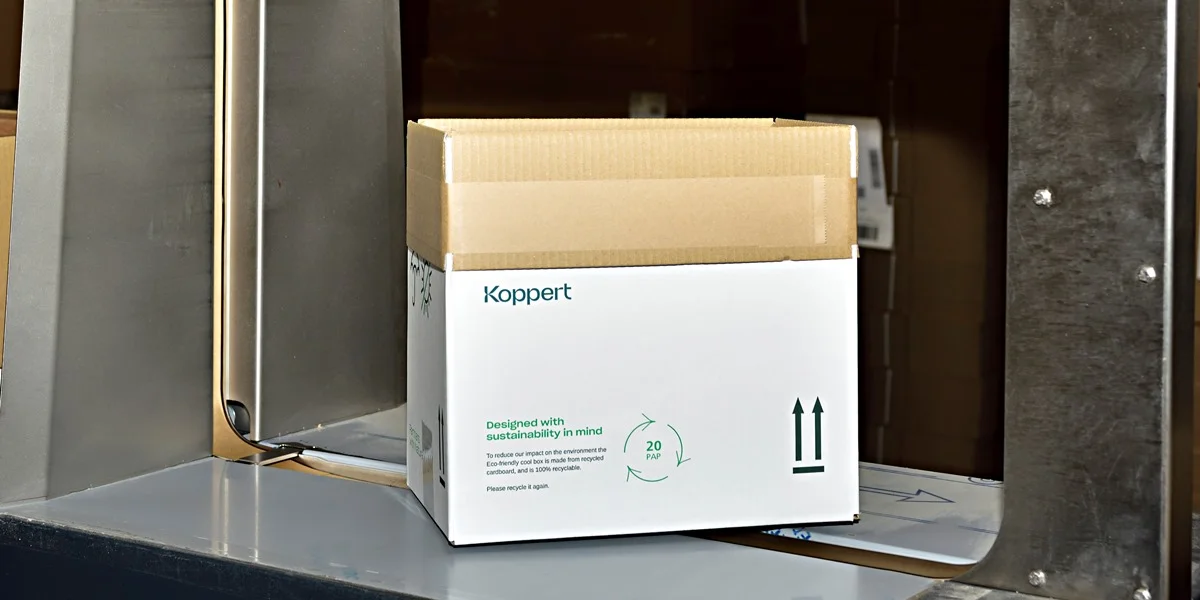
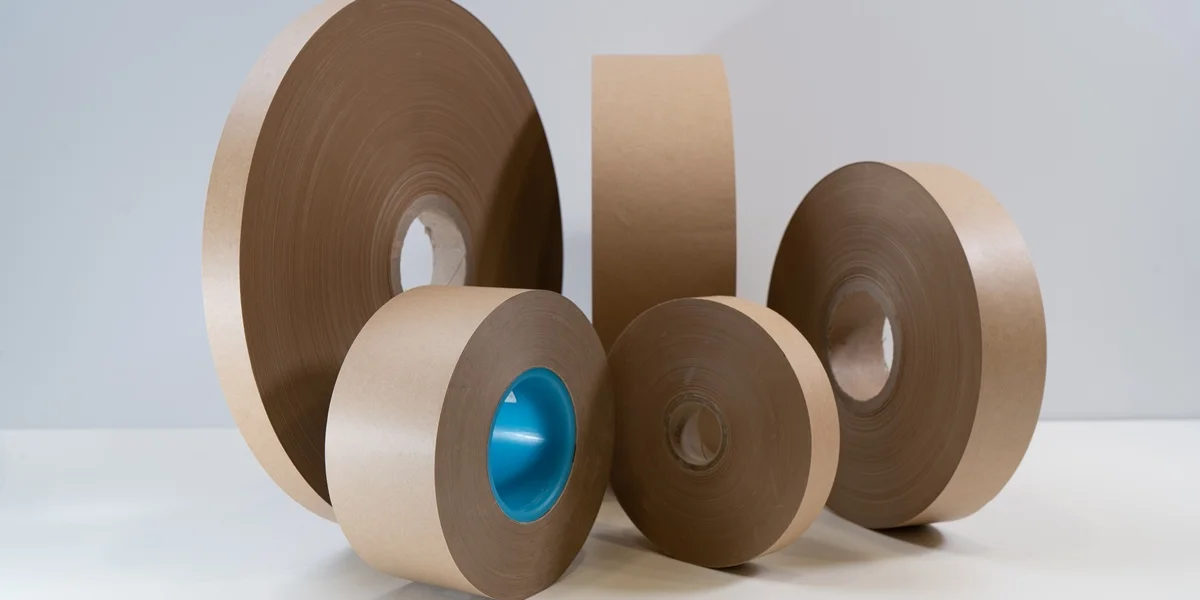
Bind tightly, work quickly
BVP wants to help its customers as best as possible and started looking for the desired solution. A suitable solution meant that the flaps of the boxes are quickly fixed in the required position and that the material can easily be removed again. Elastics and plastic did not meet the requirements, as these materials show stretch. As a result, the flaps do not remain tight against the side of the box, leading to problems with stacking and transporting.
Eventually, EVP found the solution in the shape of a Bandall banding machine, with paper bands. A paper band does not stretch and therefore binds the flaps tightly against the box. Moreover, banding is a fast process and after filling the box, the paper band can quickly be removed with one single movement.
Fully sustainable
BVP's proposal fully complied with Koppert's sustainability objectives. The Papercooler is made of paper and cardboard and makes the use of plastics unnecessary. Moreover, 85 per cent of the paper and cardboard consists of recycled material. Only the outer layer of the cardboard is made from new material. This is necessary to achieve the required strength, as paper loses some of its strength each time it is recycled. The strength of the Papercooler is excellent; the boxes have been extensively tested and passed all tests, such as drop tests and ISTA tests. Bandall contributes even further to the sustainability ambitions because BVP uses Bandall bands that are made of recycled paper.
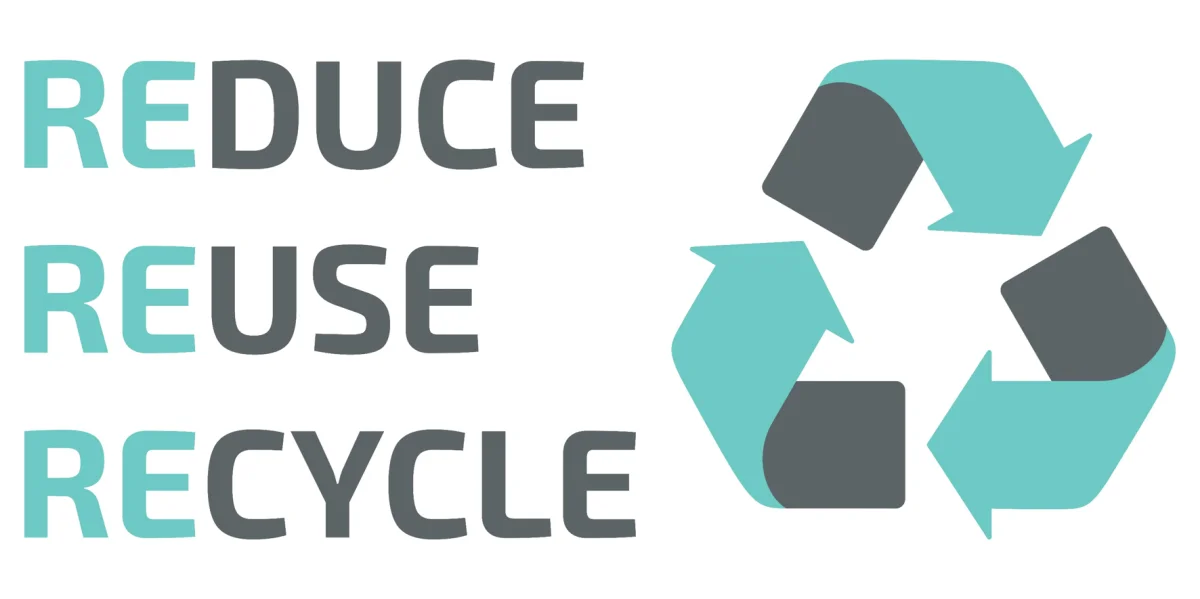
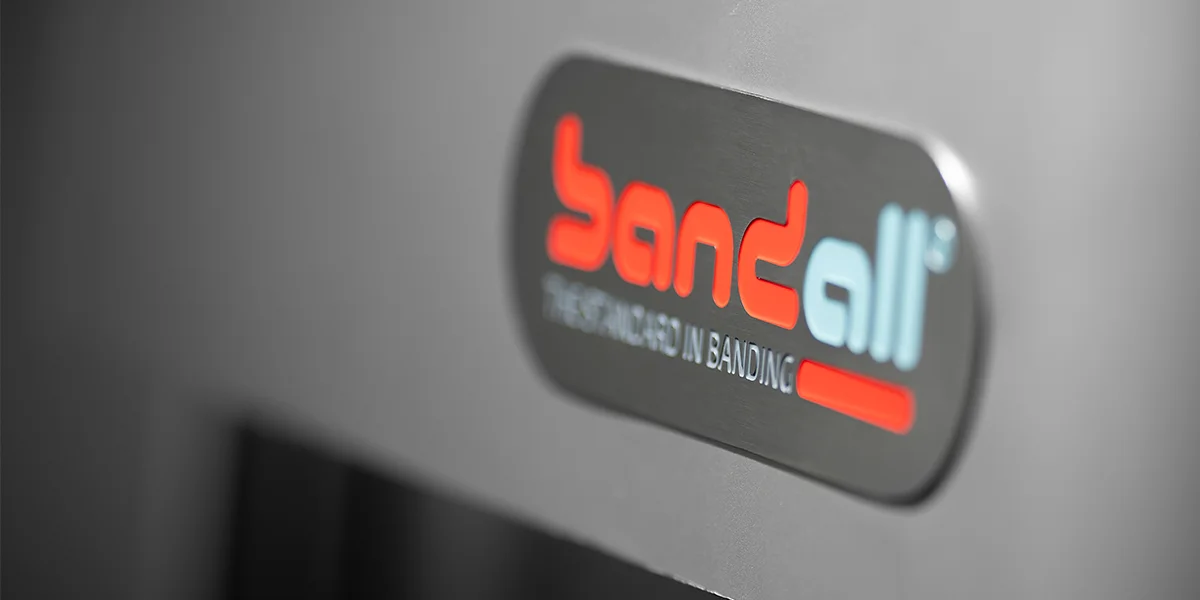
Collaboration with Bandall
Bandall is a familiar company in BVP's extensive network, and Eddo Bakker (Sales Team Manager) had good memories of the company. Which is why he contacted Bandall when he was looking for a new packaging method for Koppert. Eddo: “Bandall enjoyed working on a suitable solution, and we immediately got to work. We carried out a few tests and the results were promising. As often happens, a few minor changes were done at the last minute. When those became known, I immediately called Bandall, and they helped me straight away. I put five boxes in my car and immediately drove to their office in De Meern. That flexibility is characteristic of Bandall and is one of the reasons why our cooperation was so pleasant”.